Screen Printing!
No, this doesn’t involve the PrtScn key on your keyboard, I’m talking about Screen Printing— traditionally/colloquially referred to as silkscreening —squeegeeing ink through a stenciled textile mesh to print an image!
I’ve been wanting to develop the capability for a while, because it has uses in almost anything you can imagine. But for one reason or another it’d never materialize. Well, I finally fixed that…and I can’t even remember how that happened… I just have the stuff now, haha!
Anyway, I figured the first thing I’d do, is print something on the canvas cover we made for my 7×10 lathe.
I’ll detail the process, after the jump!
First, you need some artwork. I fired up Adobe Illustrator, because I’m totally awesome with it…
Using the Cut/Plot plugin for Illustrator that came with my CraftRobo, I set up to cut my design into some Rubylith.
This was a second try, I had screwed up the first one because I got impatient with the Rubylith, also it turned out my CraftRobo was desperately in need of a new blade and that was causing quality problems as well. Rubylith, by the way, is an old-school graphic arts material used for making hand-cut films for photographic techniques. In this case, I am going to use it as a film positive for exposing the photo-sensitive ‘Diazo’ emulsion on my silkscreen. (I really can’t -not- call it that, even though it’s not silk these days, and I don’t think it ever -was- in my lifetime…)
This is the magic that is Rubylith; it’s a light-safe red emulsion deposited on a plastic film backing. You lightly cut the outlines of your artwork into it, and peel away the unwanted parts. I love being able to do this, because it means 100% perfect vector-based output from Illustrator.
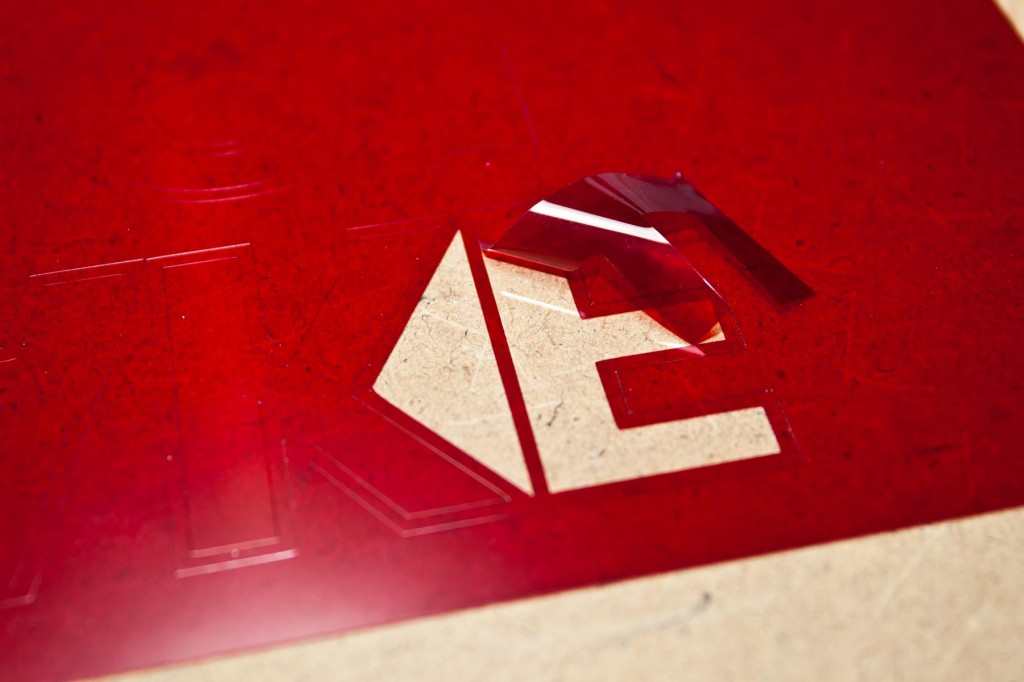
The Rubylith peels easily on a simple design such as this one… I’m still getting the hang of it though, and so far I keep screwing up the ‘weeding’ of more intricate designs. Probably for need of a proper tool.
The screen is stretched in a frame, and coated with a photo-sensitive emulsion. The emulsion blocks the gaps in the screen mesh, but until it is exposed, you can still rinse it right off with warm water. Using the Rubylith film positive I just made, a piece of glass to hold it down, and a bright light, I get to the exposing of the frame.
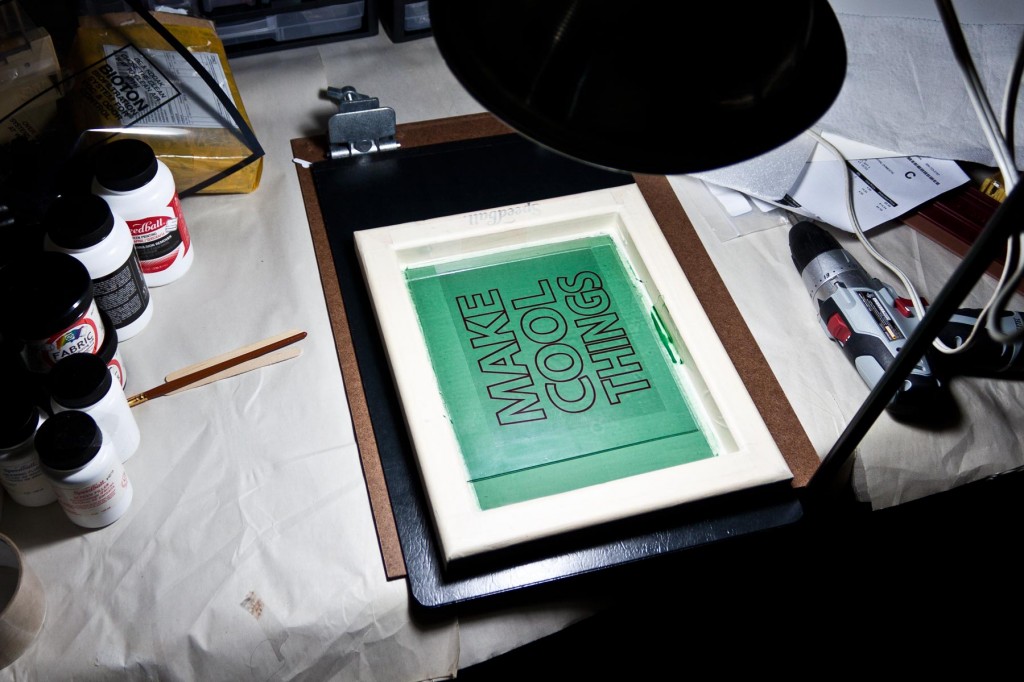
Terribly thrown-together screen exposure rig at work. Note the green color of the emulsion on the screen. That’ll change with the exposure.
After the screen is exposed, the color of the emulsion is noticeably less saturated, and when you remove the film positive, the area it was covering will still look like it did before the exposure. The un-exposed areas will rinse out of the screen mesh, meaning that ink can now pass through that area. But before I get to that, the screen needs to dry…
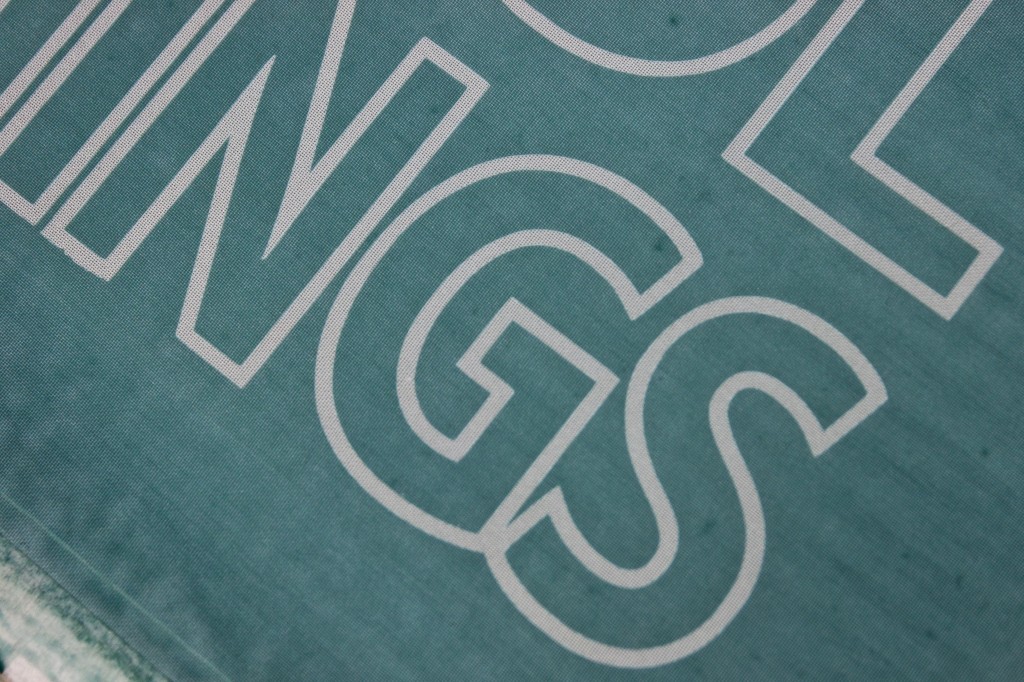
A close-up of the washed-out screen after drying, you can see the individual threads in the open areas of the mesh.
Now that the screen’s ready, it’s time to make a print! I put the screen in my simple press, spread some ink on the screen, and squeegeed it across the the surface! (In my test, it was a sheet of cardstock. Then I printed my lathe cover.)
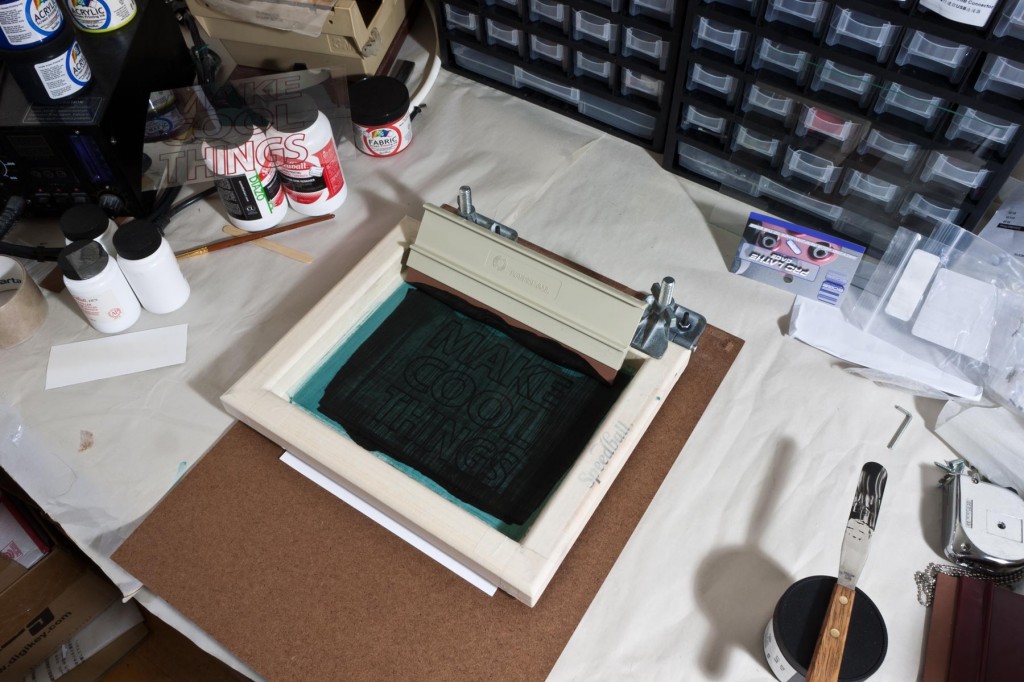
‘Flood’ the screen by doing a light pass. Then draw the squeegee across the screen again, this time with some pressure!
And that’s it! Really simple. I got this Speedball screen, and hinge clamps from Amazon. The inks are from a Speedball kit I bought. And I recently purchased a number of screens, all larger than this, and some higher resolution mesh. Expect MORE COOL THINGS in the future!